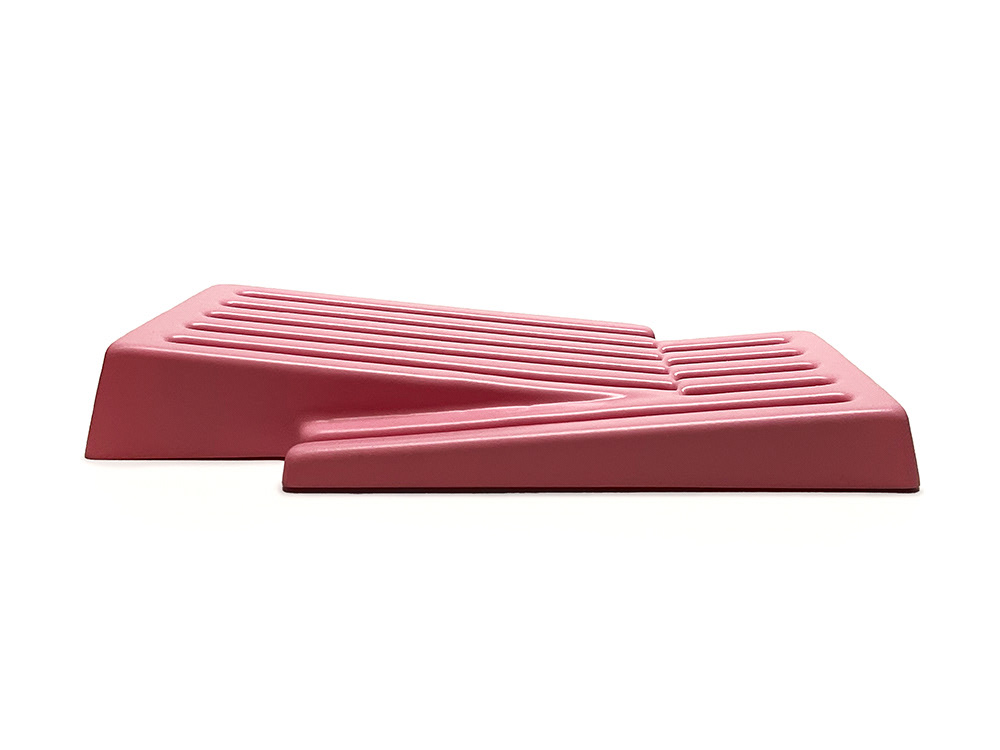
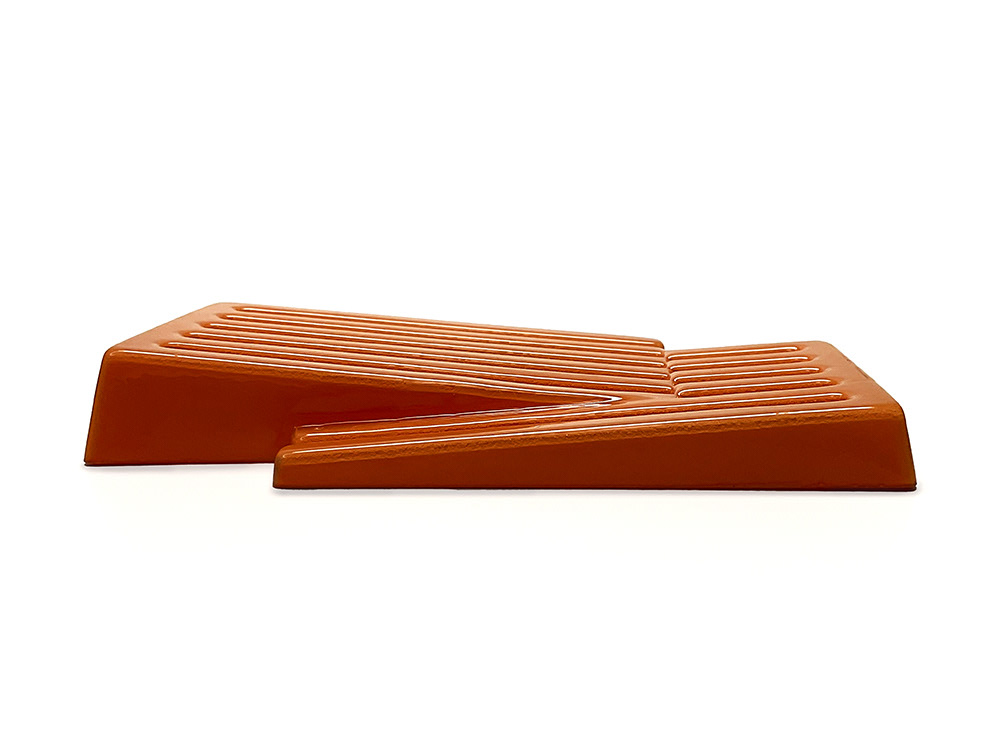
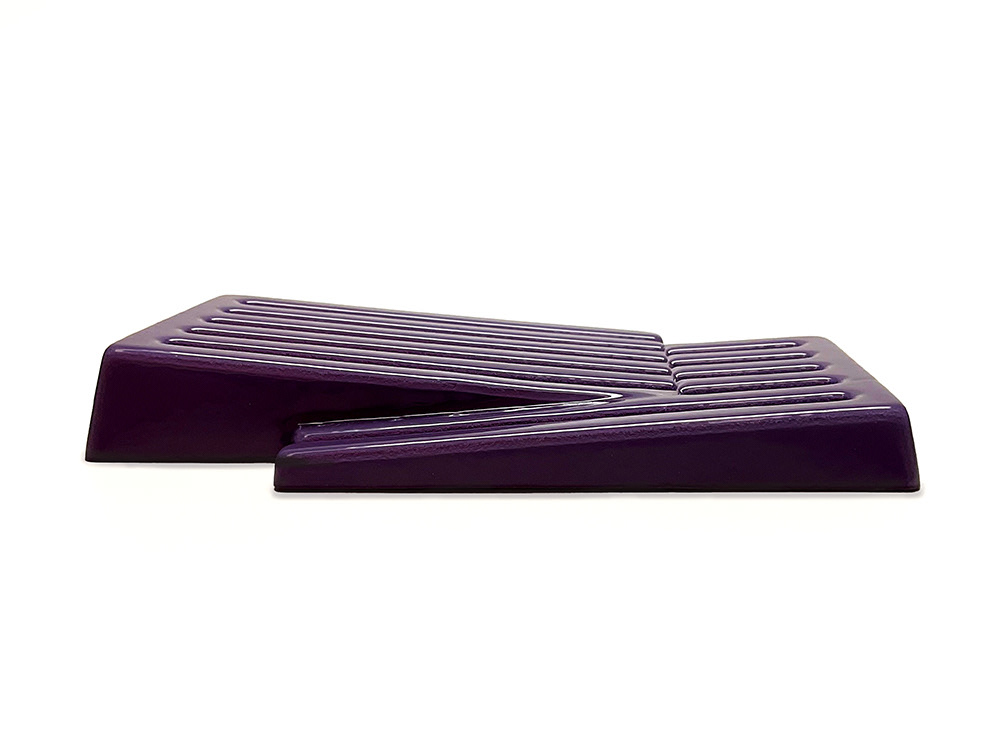
An exercise in form, soap dish incorporates the processes of milling, surface finishing, vacuum forming & airbrushing
OBJECTIVE
COMBINED ELEGANCE & PRACTICALITY
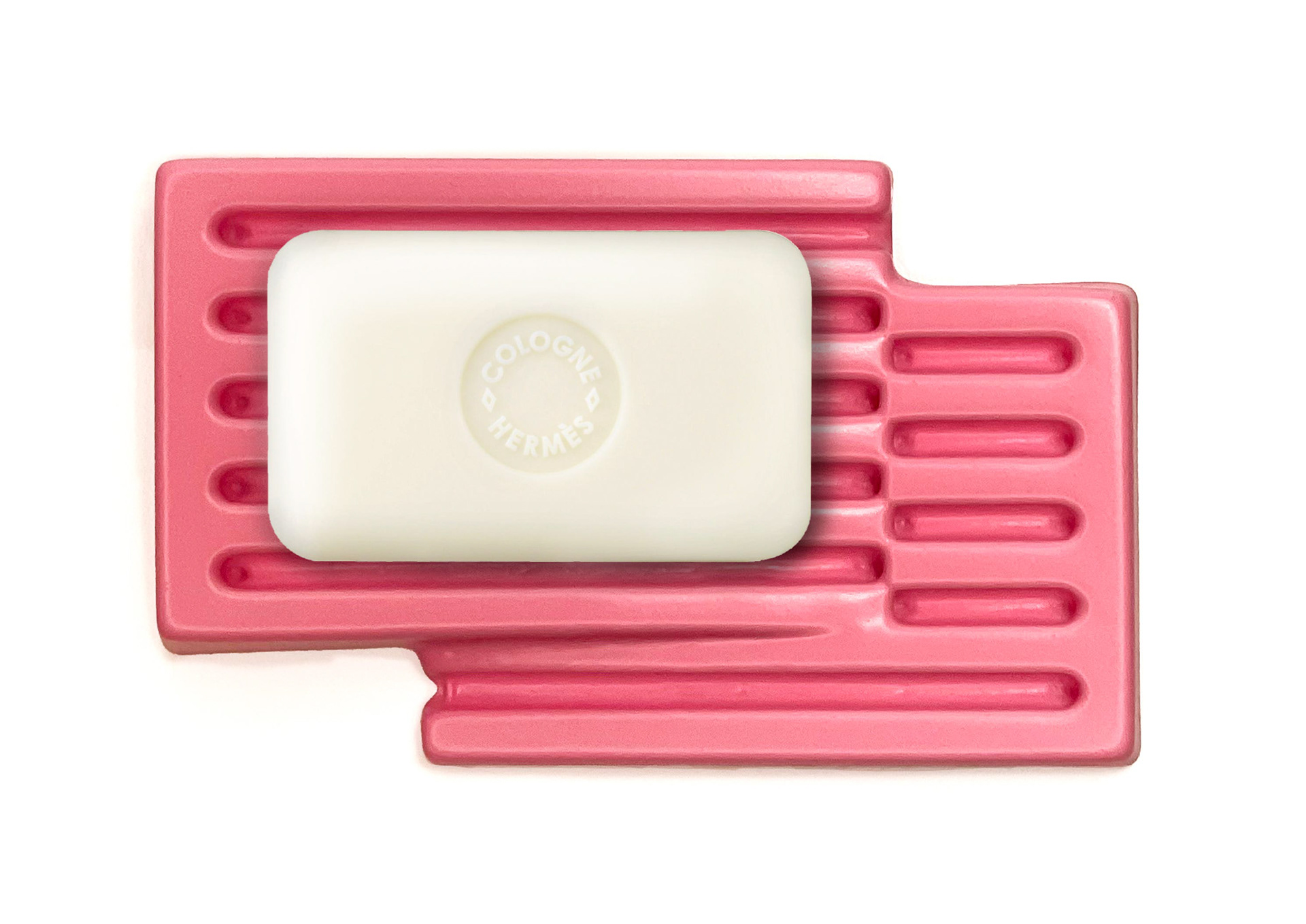
Employing the use of intersecting trapezoids, the goal of the project was to both provide a secure storage place for bar soap and facilitate drainage of the soap bar post-usage; the trapezoidal nature of the dish allowed for easy incorporation of draft angles, making production of the dish more straightforward
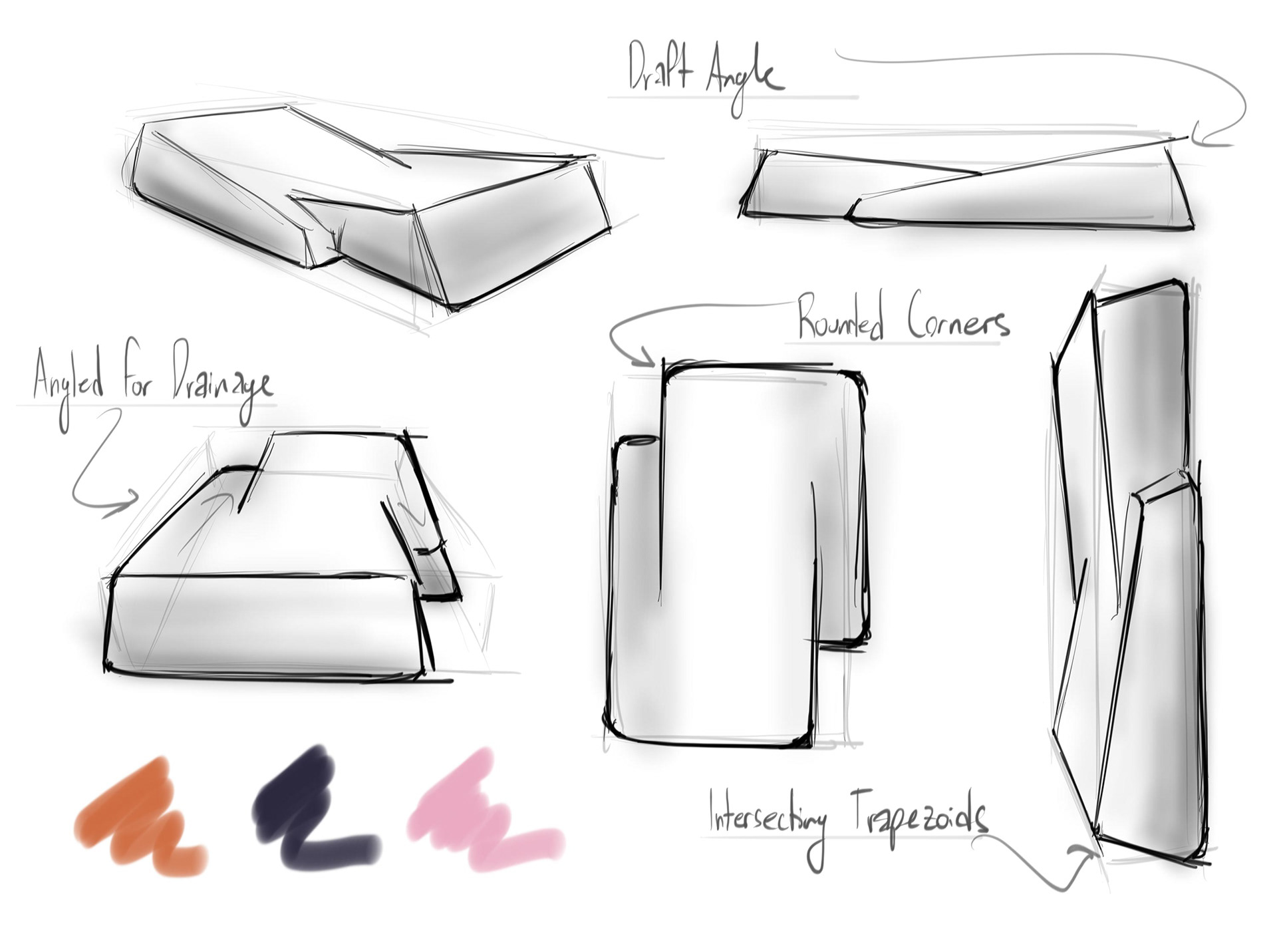
The mould was carved of 2 blocks of urethane foam on a 3 axis mill; drainage channels were first milled on each block, the trapezoidal slants cut, draft angles sanded, and finally both combined to form the final intersecting geometry
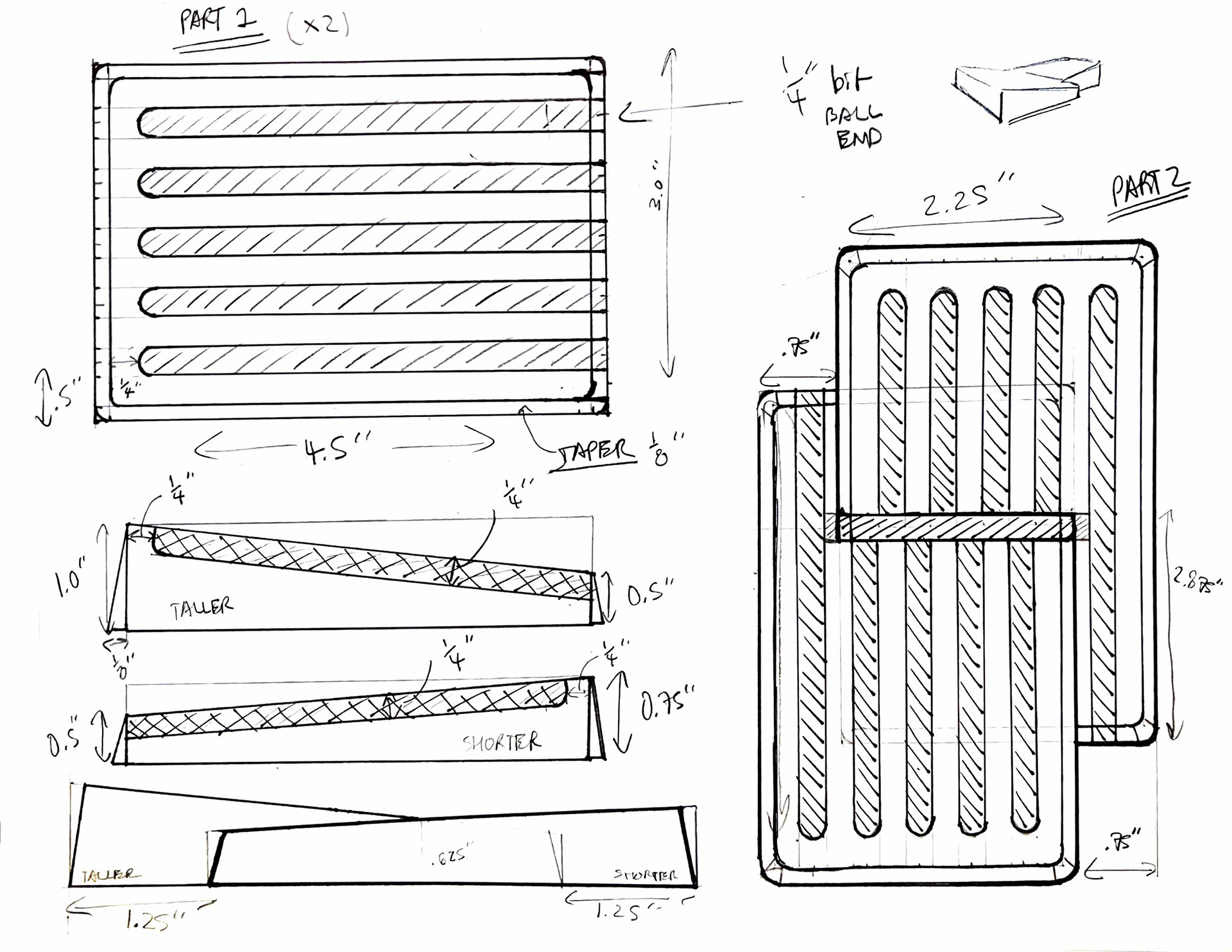
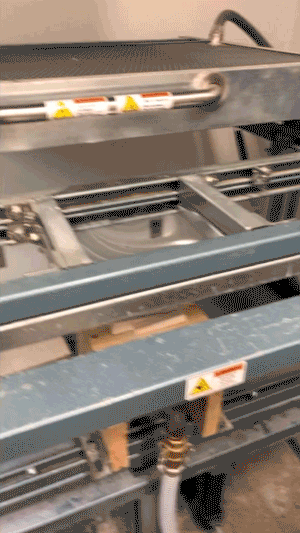
VACUUM FORMING
A PLETHORA OF ATTEMPTS
Though the mold creation proved expedient, vacuum forming proved a challenge with over 12 sheets of plastic needing to be used to yield a desired result; challenge came in the form of finding the right ratio of heat applied and timing of vacuuming
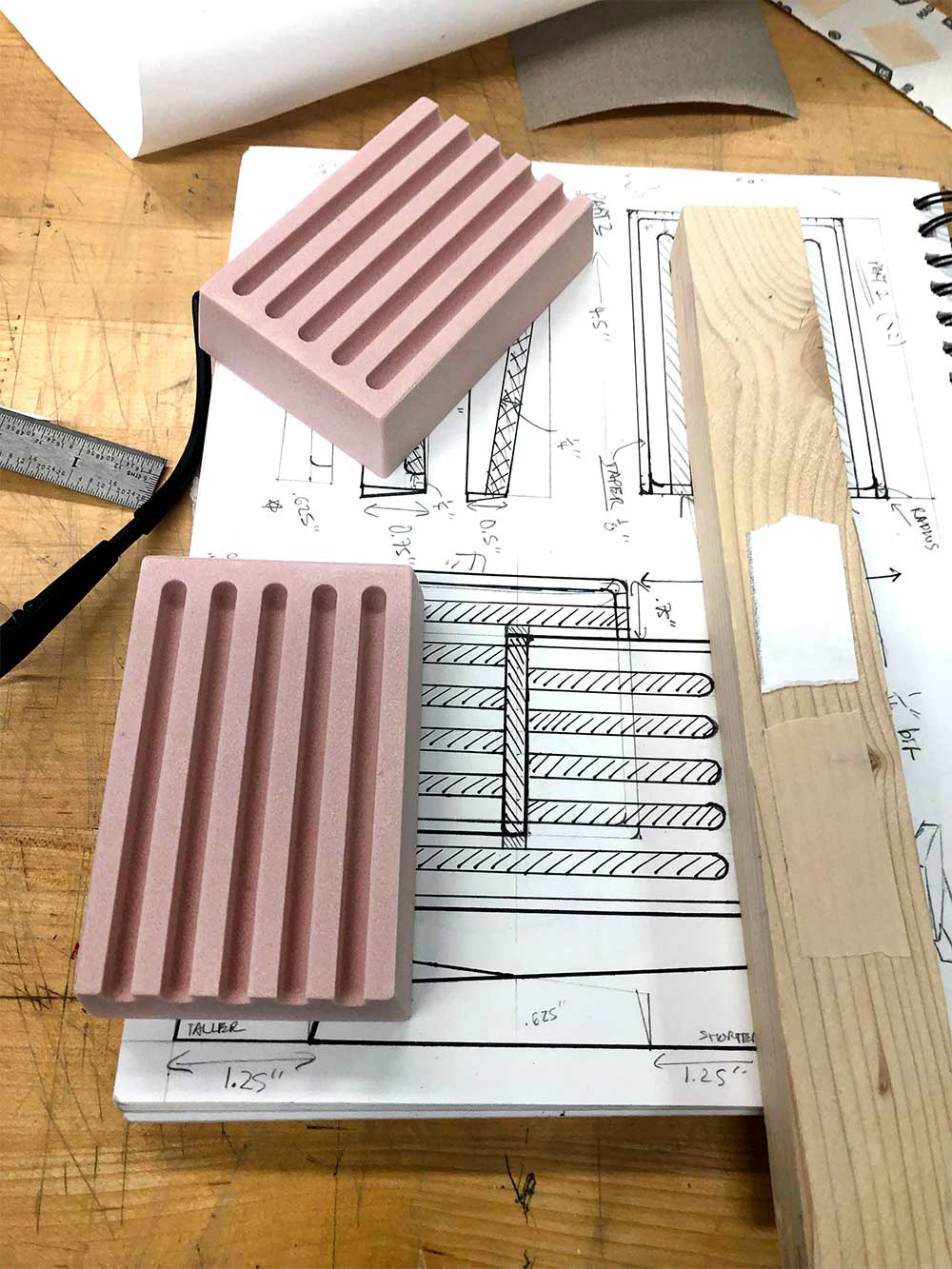
Pre-Trapezoidal Cuts
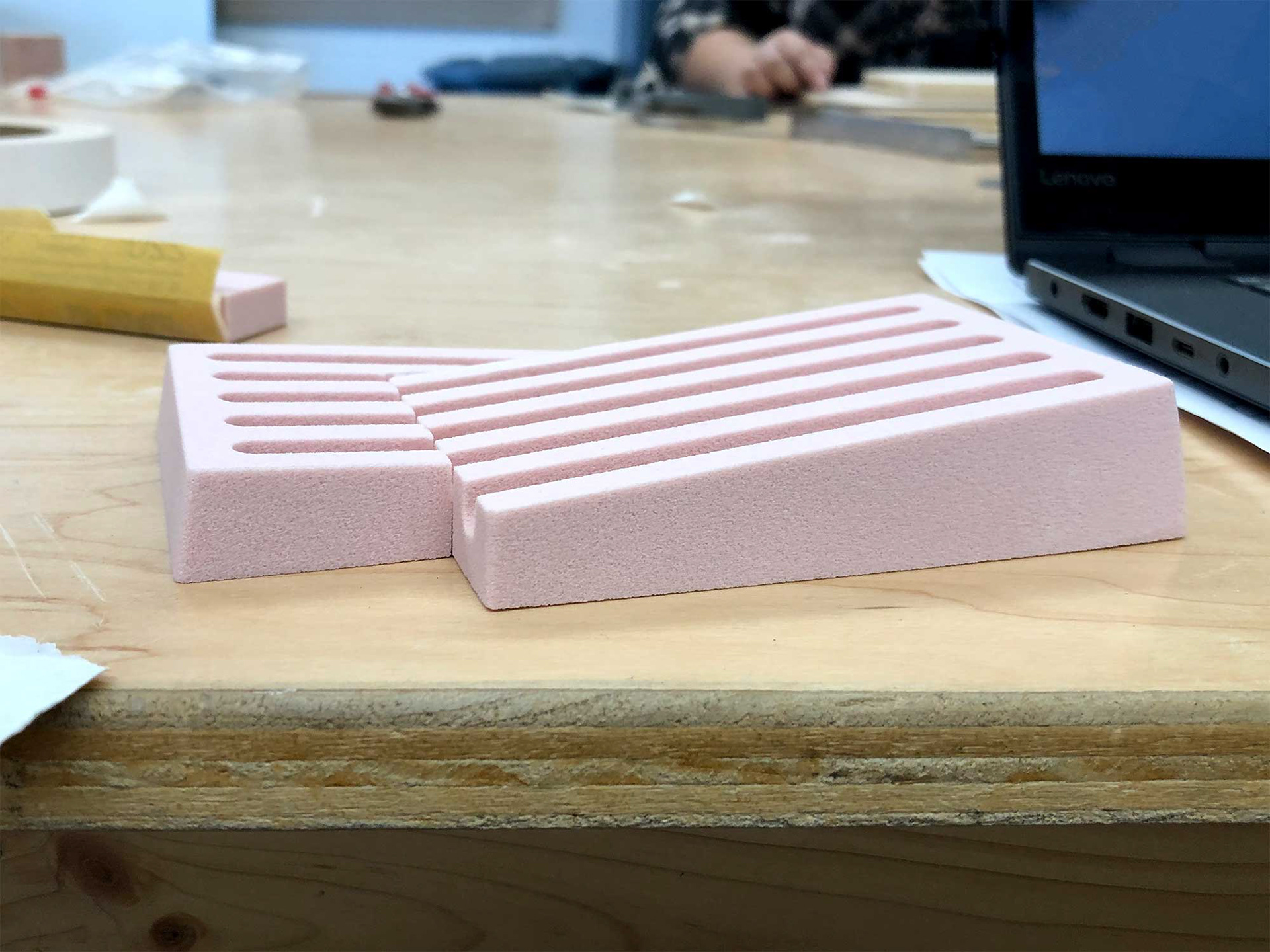
Combined Trapezoidal Cuts
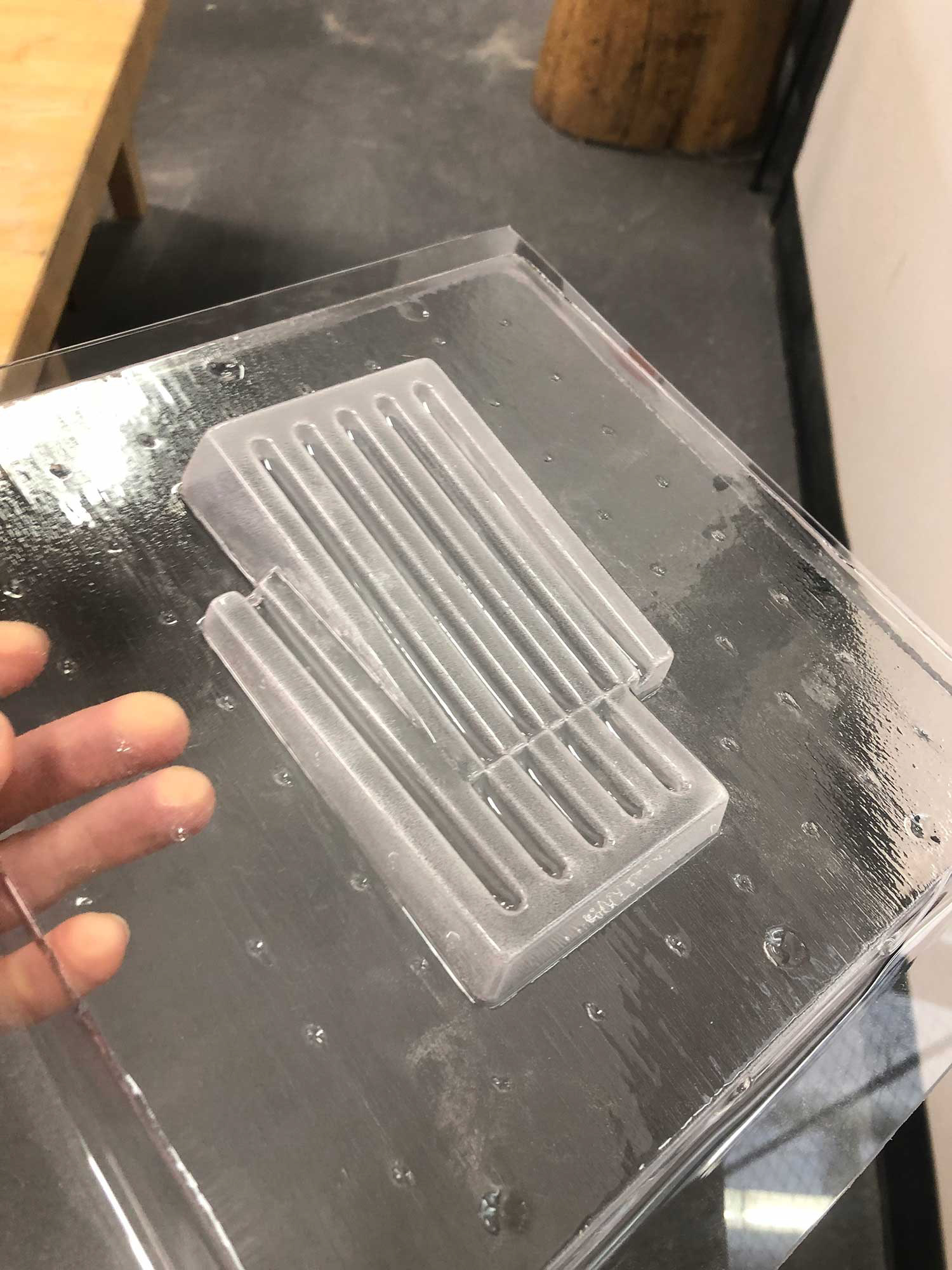
Vacuum Formed Sheet
3 final soap dish "shells" were cut free of the mold using a bandsaw, seen above in the far right, and were finished with hand sanding
FINAL
SIMPLY SOAP-TACULAR
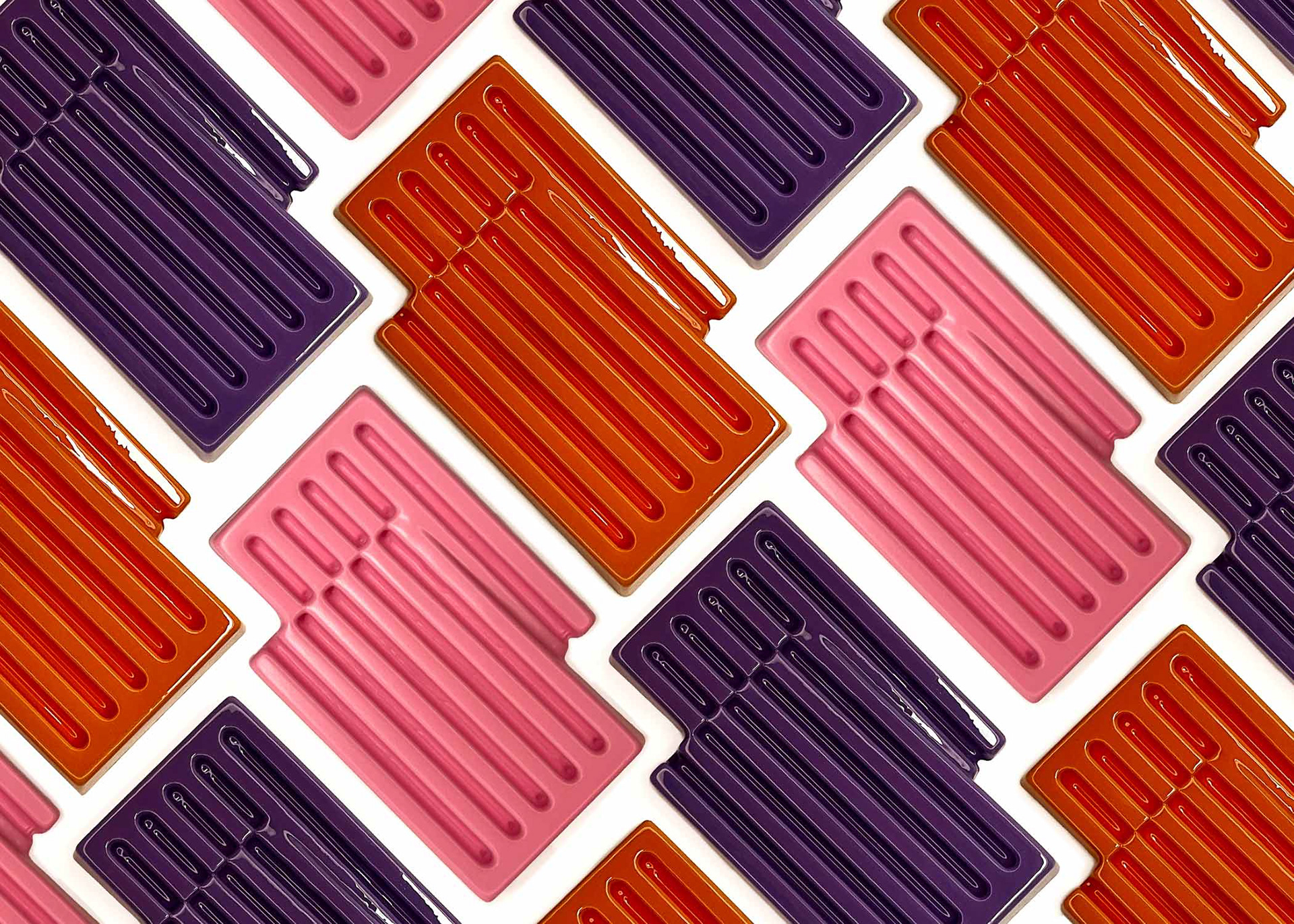
These 3 shells were then airbrushed, sealed with polyurethane, and currently reside in the various bathrooms of my relatives
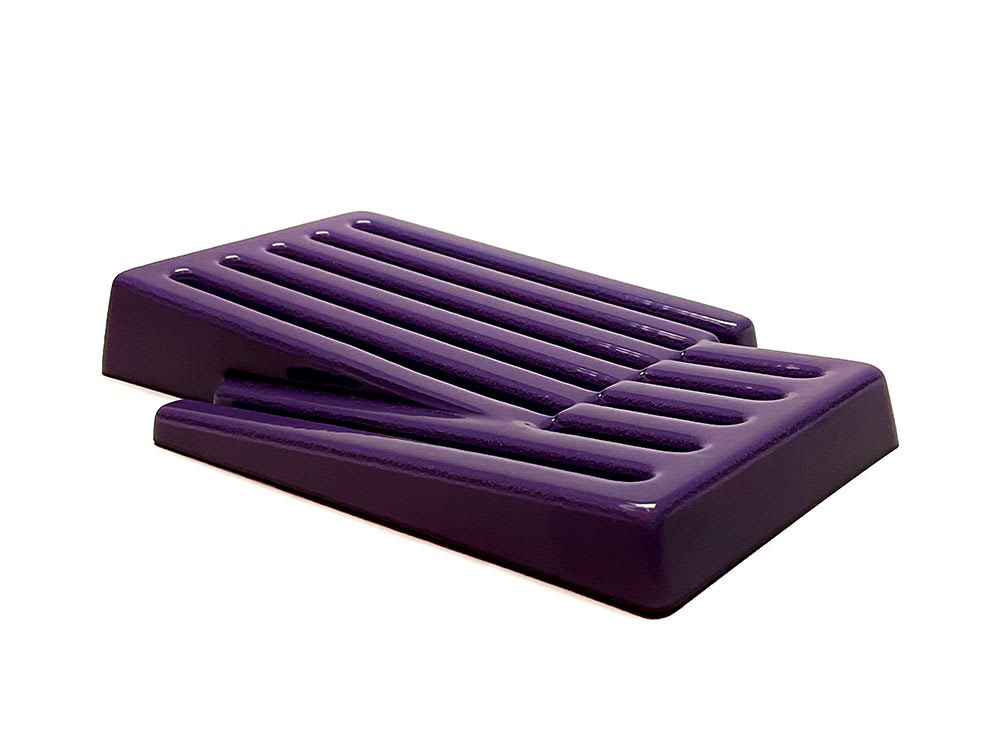
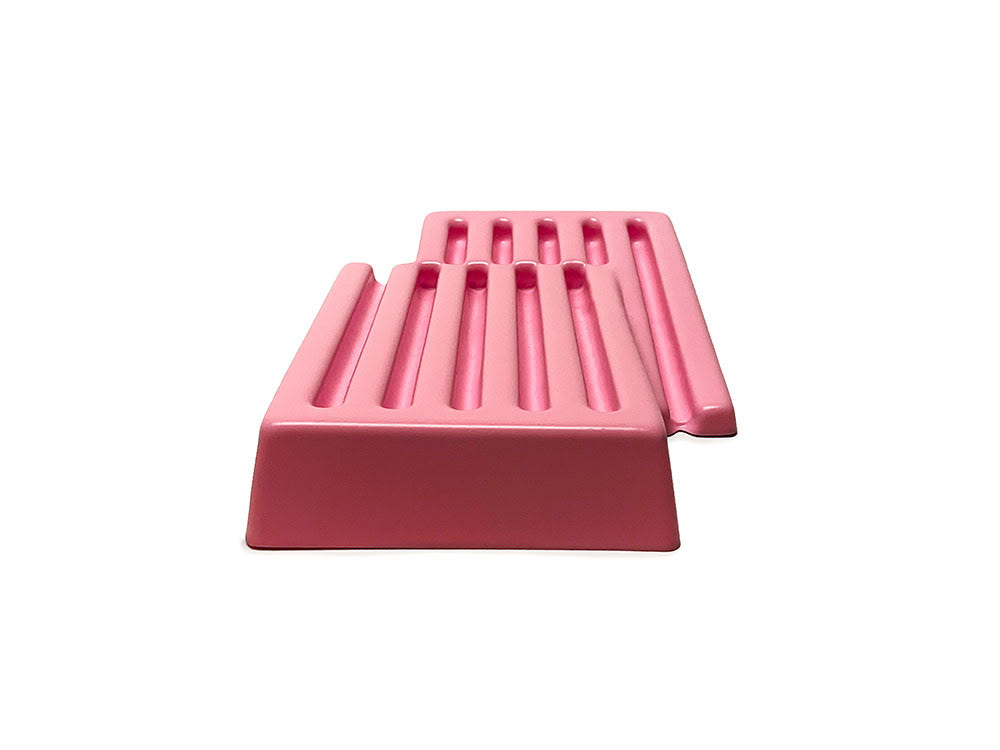
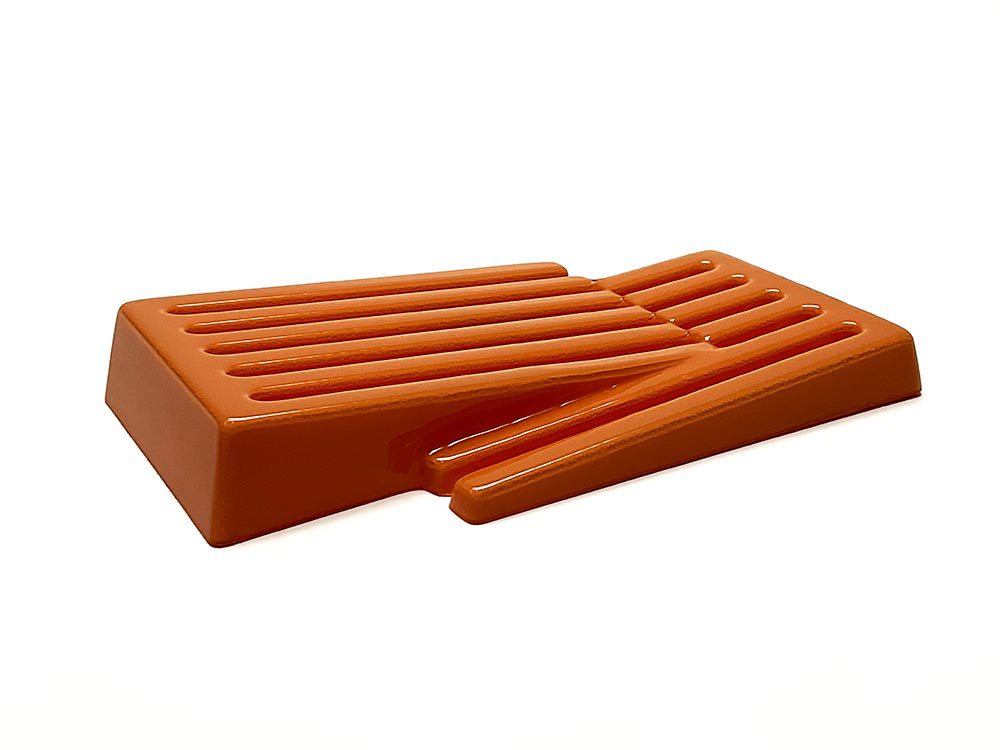
SOAP DISHES 2021 PETG PLASTIC 5.75 x 3.75 x 1 INCHES 3 WEEKS